Torque it!
To many manufacturers, the concept of torque is a mystery. Ask them to describe the physics of torque and you’ll likely meet a blank stare. Cracking open a dictionary won’t help much either. To the layman the definition reads like a foreign language that owes more to mysticism than science. Despite the confusion, proper control of this mysterious force remains a critical component for quality manufacturing and has a direct impact on the bottom line issues like product quality, reliability and safety.
What is Torque?
Torque is a “turning” or “twisting” force and differs from tension, which is created by a straight pull. However, we use torque to create a tension.
How? As the nut and bolt are tightened (Diagram A), the two plates are clamped together. The thread angle in the bolt converts the force applied into tension (or stretch) in the bolt shank. The amount of the tension created in the bolt is critical.
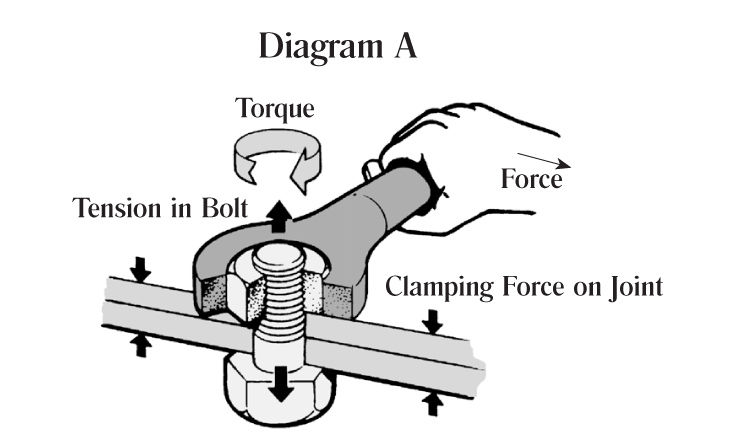
Why? A bolt tensioned properly works at its optimum efficiency and will resist coming undone. However, if the tension is too low, the nut could vibrate or work loose. If the tension is too high (overstretched), the bolt could break. Ever y bolt has a correct optimum torque/tension figure for each fastening application. It is important to have these figures available so that the end product will be safe, efficient and economical.
How do we Measure Torque?
Torque is the result of multiplying the value of Force applied by the Distance from the point of application.

Comparing the two examples, please note that the same Torque result can be achieved with a lower Force if the Distance from the nut/bolt is increased.
Another factor that affects applied torque when using torque wrenches is if it is “length dependent,” which means that the actual torque applied to the fastener varies if the hand position on the wrench is varied (even if the wrench is preset). This occurs if the pivot point of the wrench mechanism is not coincidental with the point of application of torque.
The Importance of Torque Control
The reliability of machine parts subjected to fluctuating loads and stress depends on the fatigue strength of the materials. A threaded fastener, however, relies upon an elastic interaction between the mating components. Its objective is to clamp parts together with a tension greater than any external force trying to separate them. The bolt then remains under almost constant stress and is immune to fatigue. If the initial bolt tension is too low, the fluctuating load in the shank in much greater and it will quickly fail. Reliability, therefore, depends on correct initial tension and is ensured by specifying and controlling the tightening torque.
Torque Tools
Torque is simply defined as a measurement of turning or twisting force applied to an object. Every day, screwdrivers, wrenches, impact tools and even hammers are used to apply torque on assembly lines to create the tension required to clamp bolts, screws and other fasteners firmly together. However, none of these tools can assure that proper tension is being achieved.
A manufactured product’s quality and integrity are completely dependent upon the reliability of fasteners and the elastic interaction between the mating components. The objective is to clamp parts together with a tension greater than any external force trying to separate them. The part then remains under constant stress and is immune to fatigue.
An inadequately torqued fastener can vibrate or work loose; conversely, if the tension is too high, the fastener can strip its threads. Faced with these options, manufacturers are realizing that torque control could spell the difference between a safe, reliable and economical product and complete disaster.
The precise control of torque is a key to a quality assembly and can ensure that products perform as expected. In many cases, before finished products even reach the market, companies have spent a great deal of time and money for disposal or repair of damaged parts, during assembly, which are the results of improper application of torque. Even worse, if these products (albeit unintentionally) make it to market, manufacturers are faced with customer dissatisfaction when products fall apart due to loose screws or stripped threads.
Manufacturing costs may also be reduced through precise torque control. For instance, Seagate, a manufacturer of computer hard drives, initially utilized Mountz tools to maintain critical assembly tolerances, but realized additional saving when the number of drives that had to be scrapped or reworked, due to over tightening, was reduced.
Product safety and related liability exposure for manufactures can also be dependent on the proper utilization of threaded fasteners. In critical applications where safety is an issue, the proper use of fasteners can decrease the incidence of expensive lawsuits and product recalls.
Reducing worker fatigue also has to be considered in achieving production line consistency and reducing the lost time costs associated with repetitive use injuries. When fatigue occurs due to high repetition or strenuous effort, torque control tools are available which improve ergonomics and reduce the effort for consistent torque application. When planning a production area, it pays dividends in the long term to plan the ergonomics of the operation and consult a health and safety inspector or ergonomic manager. Ensure both the workplace and the assembly operation are compatible with the majority of operators who will work there. This can reduce future costs arising from work-related health disorders among operators, along with costs arising from poor product quality. Also, the need to redesign the production system later may be avoided.
A wide variety of tools are available to control and measure the amount of torque applied to fasteners. These “torque control tools” utilize calibrated torque setting mechanisms that may be factory pre-set, or user-definable. When the specified torque setting is reached, the tool provides a visual, audible, or tactile signal.
For low production applications, or to verify torque out in the field, manual torque wrenches are available that may have dial indicators, emit an audible click, or slip when the specified torque value is achieved. Manual torque screwdrivers work on the same principle by providing a slipping sensation when the specified torque is reached. Electric or pneumatic screwdrivers can be incorporated into workstations to speed up production and reduce repetitive motion injuries and carpal tunnel syndrome.
For large fasteners in industrial applications, manual and powered torque multipliers are often used to replace impact wrenches. Torque multipliers are available that can deliver over 30,000 ft. pounds of torque, with precision.
Another variable to be considered is whether torque will be applied statically or dynamically. Static torque is applied by hand and occurs relatively slowly. Dynamic torque is applied with a power tool at a high rate of speed. More tension is normally generated by dynamic torque than static at a given torque setting, because of the momentum generated by the tool’s motor and gear assembly (inertia) and the lower coefficient of friction.
Varying loads and vibrations represent a special challenge for threaded fasteners. Since a properly torqued threaded fastener is always under steady tension in connecting two mated components, it is virtually immune to fatigue. However, if the initial bolt tension is to low, the bolt will vibrate loose or break and the joint will quickly fail.
When determining correct torque specifications, the engineer must take several more variables into consideration. The first consideration is the maximum load that may be placed on the fastener, the second consideration is the strength of the material that is being joined and the third consideration is whether the joint is hard or soft. A hard joint connects materials together directly. In this case, the fastener rotates very few degrees, after it comes in contact with the material, to develop full clamping force. A soft joint might contain a gasket. In this case, for the same torque setting, a fastener goes through more degrees of rotation before it generates full clamping force.
Using a quality torque tool makes a safer world through accuracy and precision. Controlling torque is essential for companies to ensure their product’s quality, safety and reliability isn’t compromised. The failure of a three-cent fastener that isn’t properly tightened can lead to catastrophic or latent failures. Fasteners that are insufficiently fastened can vibrate loose and excessive torque can strip threaded fasteners.